September 5th, 2014
admin
End mills come in all shapes and sizes. There are many different systems for securing end mills but all operate on the same premise, tight hold. My mill has a morse taper of 3 also known as MT3. I decided to purchase a collet set as this was in my case least expensive. You can opt for MT3 collets instead of a collet chuck however the process of changing them is the same as removing / installing the collet chuck. If you need to change collets regularly, a collet chuck is quickest. Why not just use a drill chuck to hold the end mill? This will result in movement of the end mill which will affect the finish of the job. The collet holds everything tight. My collet set goes up to 16mm which does most jobs. For my 20mm end mills, I need to buy a collet that will go into the spindle direct.

This is my collet set. It contains collets, a collet chuck and a collet chuck key.
|

This is a collet.
|

The collet is tapered so that when the chuck is tightened, the collet is pushed back into the collet holder causing it to compress. The compression force secures the end mill.
|

The collet chuck is basically a hollow nut that screws over the collet and onto the collet holder. The nut then pushes the collet back into the hjolder causing it to compress into the direction of it’s axis.
|

This is what it looks like when you fit a 12mm 2 flute end mill.
|
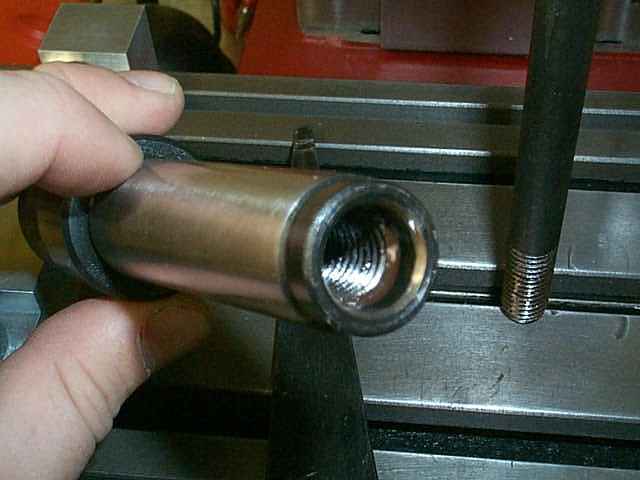
The other end of the collet holder has a threaded hole in it. This threaded hole points upward when the holder is inserted into the milling machine spindle. The drawbar is threaded into the hole.
|
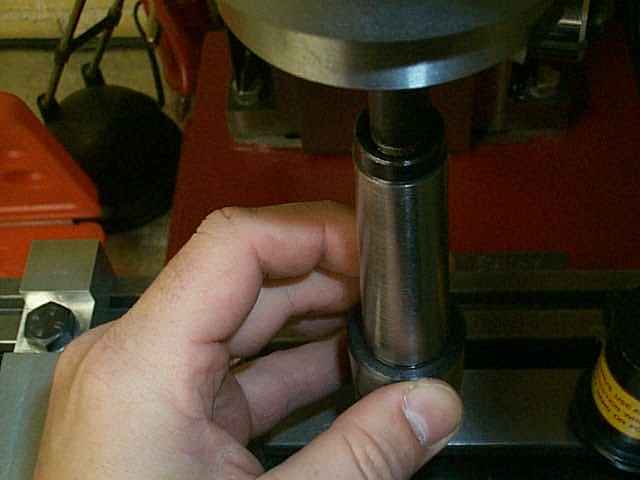
Threading the drawbar into the collet chuck before pushing the assembly up into the spindle. The black thing on the right is the cover for the splined shaft in the picture on the right.
|
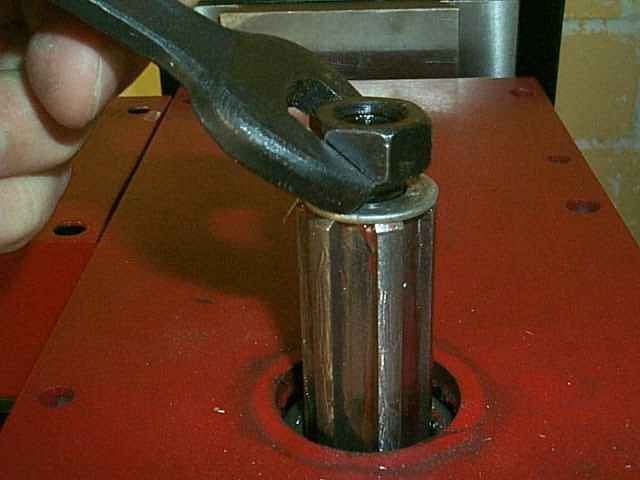
Once the assembly is pushed up into the spindle, the draw bar pockes out of the spindle drive shaft. A washer and nut is fitted and the whole thing tightened. The nut pulls the draw bar up and this brings friction forces against the taper of the spindle. The tighter you tighten the harder it holds. There is no need to tighten too hard anyway as the taper holds well with little force.
|
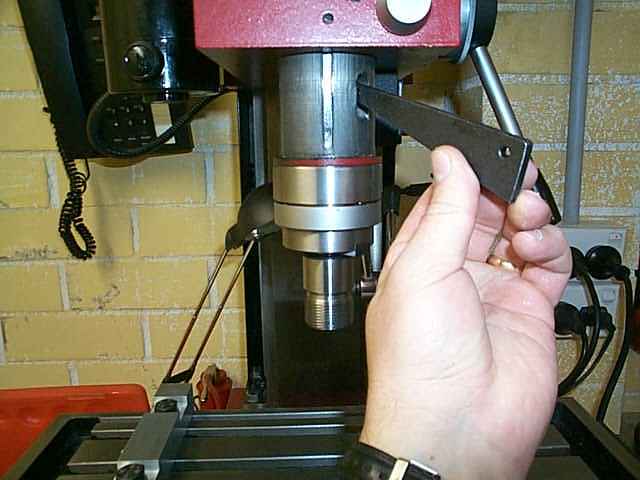
I normally stick this wedge in a hole in the spindle shaft to lock it whilst tightening the nut or the collet chuck.
|

Left or righjt handed. I am a really talented person. LOL.
|
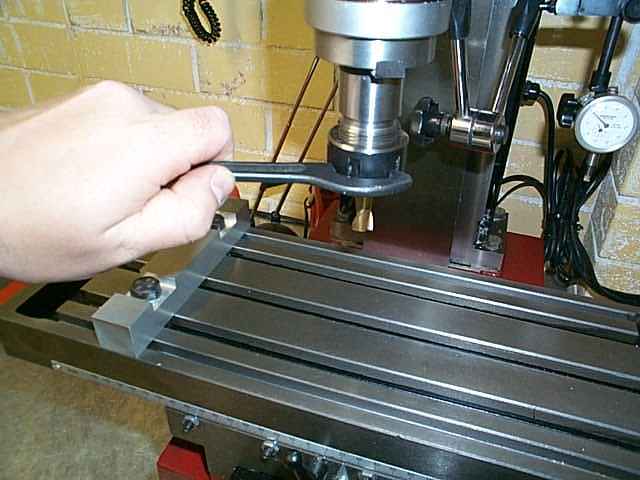
Finally, a tighten of the chuck and your off.
|
|
September 5th, 2014
admin
4″ Rotary Table Setup
t has been a long wait of 10 weeks but finally it arrived, by boat. My rotary table with dividing plate and tailstock. The folks over at the Little Machine Shop have a wonderfull range of products, this being one of them. All up it cost me about $370AUD with shipping.
This expose will deal with the unpacking and clean up of the components. I will try and work out how to use it over the coming weeks and add an article to the documentation section

It is finally here, a box from the USA…can it really be the rotary table? I had waited such a long time for this day to finally arrive.
|

Inside were thre boxes and a heap of statically sensitive foam fill. I used the vacuum cleaner to assist in the unpacking operation.
|
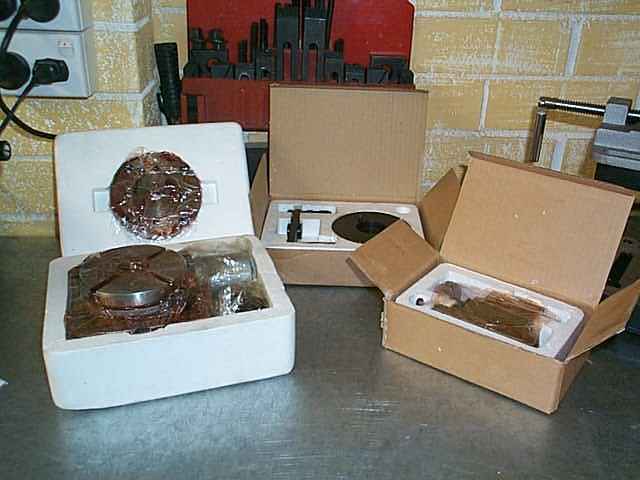
Everything was well wrapped in plastic and preserved in red grease. It could probably sustain many millions of years of mummyfication due to the grease.
|

Now how does this sucker pull to pieces?
|

There is a screw on the bottom that locks a vlack threaded ring. Remove the screw and unscrew the ring.
|
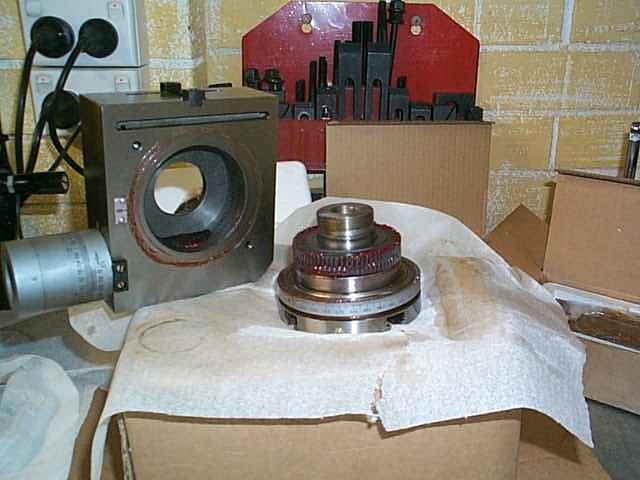
The rotary table should now ease out of the base with very little force. Grease everywhere.
|

There are two grub screws that keep the vernier locked into the base. Remove them and gently twist and pull until it is free.
|

The grease is hard to remove from the rotary table’s gear teeth. I opted for a brush with plastic bristles. Wear eye protection to avoid red grease eye!
|

The dividing plate is tricky. There are many holes and they are all full of grease. Patience is a neccessity.
|
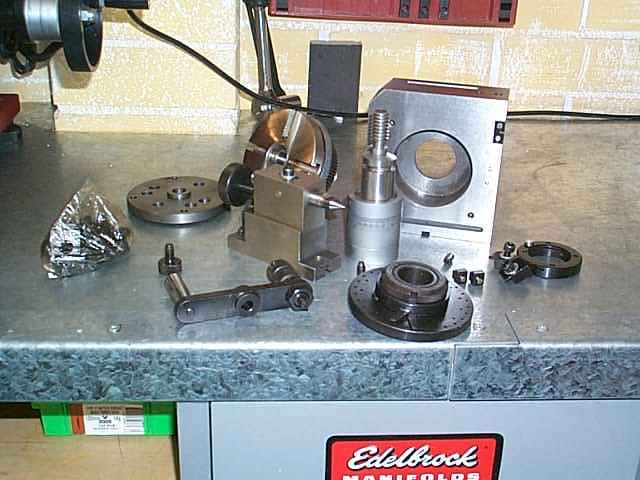
Look at all those clean and shiny components. It is a real treat to run a clean workshop.
|

Here is a shot of the gears re greased with BP lithium grease, same as the mill. Not red but green.
|

Anybody getting turned on yet?. Shiny = Sexy!! I have stuck it on to see how it fits.
|

Different angle.
|

The clamp on the rear. See the black ring with a screw in it, that’s what I spoke of earlier.
|

And yet another angle.
|

Leftovers? No, this is the rest of the stuff, indexing plate and T-Nuts, bolts etc.
|
September 5th, 2014
admin
This is my 110 Piece Tungsten Alloy Tap & Die Set. I am able to create threads for holes or bolts up to 18mm in diameter. Drill a suitable hole and use the appropriate tap to install a thread for your bolt.

This set has two layers, the taps are on top, the dies are under.
|

A pic of the dies.
|
September 5th, 2014
admin
SIEG Industries X3 Mill / Milling Machine and Drill. The Super X3 will be updated shortly also. This is the same machine sold by Hare and Forbes HAFCO and by grizzly and harbour freight in the USA. My take on it and the experience of purchase.
Ths is my Milling Machine. Assembled by Sieg Industrial in China and purchased from , of all places, a woodworking specialty store. Amazing what you can find when you look in all the wrong places. This Mill goes by the name of the X3. This machine is the next step up from the mini mill. The mini mill is called the X2 and is sold by Hare and Forbes in Australia or Harbour Freight / Grizzly in the United States. The Mill is capable of 25mm drilling / end milling or 50mm facing. This is more than enough for most small projects.
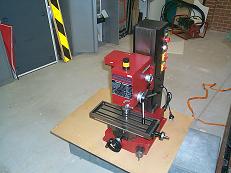
Fresh off the trailer. This was a showroom floor model so it did not come crated. It still has gunk and red grease all over it.
|
|
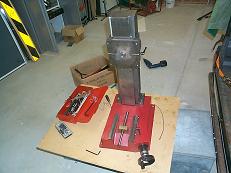
Mostly a naked machine. Only the column and base are intact. At this point I decided to separate the column from the base and clean everything. The possibility of a new paint job is on the books too.
|
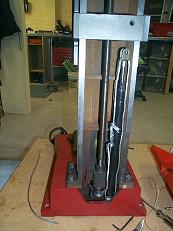
The column has a loaded gas strut. BEWARE!
I secured the strut with a piece of fencing wire. There is a screw top and bottom of the gas strut, note the hole in the head screw block.
Secure the strut before you release the screw from the strut. The column is then free to remove. Release the four bolts on the bottom.
|
|
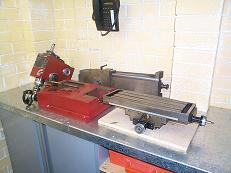
Here are all the main components laid out ready for thorough cleaning, lubrication and assembly
|
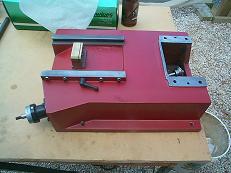
It is important to have plenty of wipes on hand and a can of WD-40. The base is easy to clean.
|
|
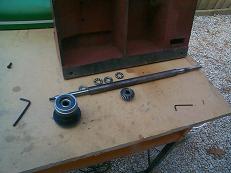
The Z axis was removed as it felt very heavy despite having no load to move. There are bearings in the housing adjacent to the Z axis handle and a brass bush at the other end near the column.
The bearings were gunked up with dried grease and the grease in the bush was sicky. Everything was treated to a turpentine bath.
|
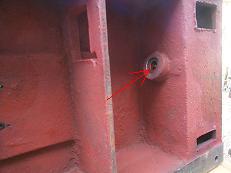
I noticed the Z axis bush near the column had an oil tube installed. I investigated the top side to try and find the oil point.
|
|
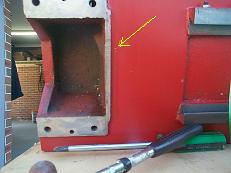
I found out why at first I did not see this oil point. It was covered by paint. I subsequently removed the paint and tested but found it clogged.
Compressed air and a fair bit of poking did not resolve the blockage. Looks like this oiler is a dud.
|
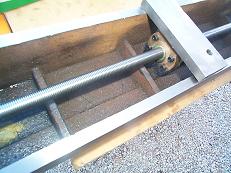
The Z axis screw was cleaned. There was a lot of dried grease in the thread. New grease was applied and the screw was run from end to end.
I connected a battery drill for this operation as it would take forever with your fingers.
|
|
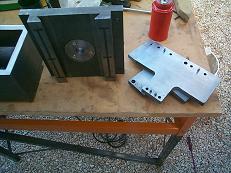
Here is the cleaned up head mounting assembly. This is one rigid mill. The quality of the casting is quite reasonable for a low cost machine.
|
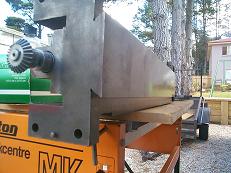
Here is the cleaned up column. Stamped as number 25……..wonder who has number one?
|
|
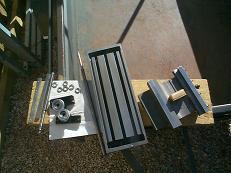
The compound slide took a while to clean. There are plenty of bearings. My only gripe is the quality of the circlips used to secure the stop washers at the end of the XY screws. Cheap Cheap Cheap.
Looks like they are made of mild steel not spring steel. Spread them and they permanently deform.
|
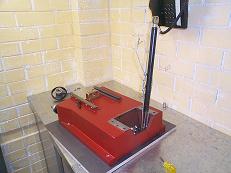
Remember the strut? I put it back onto the base before adding the column.
|
|
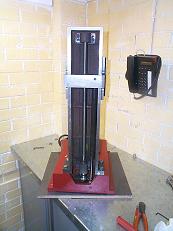
The Z axis gear assembly at the base of the column posed an issue during installation of the column. I had to shift the gear on the horizontal shaft back a few millimetres before once again adding the column.
At this point I installed the dovetail head slide and thoroughly lubricated all contact surfaces. The top gas strut screw was reinstalled. Pressure was relieved from the strut and the wire cut and removed.
|
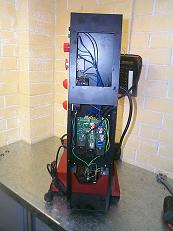
The rear column cover and electronics was added. This is a great setup. Very easy to remove if you need to work on the circuit board. This particular model did not ship with the fan installed so I will add my own at a later time.
A fan will be ideal when using the mill at extremely slow speeds under heavy load.
|
|
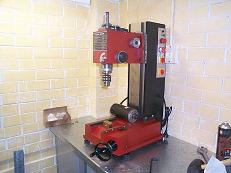
The head was added. Make sure you have a bolt ready. Once the head is positioned onto the round protrusion on the rear mounting plate, it is easy to keep it there with one hand and install one of the top screws. Don’t forget to add the other 3.
The motor was added next.
|
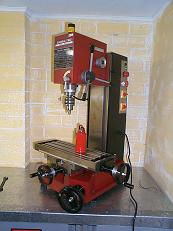
Voila.
Clean and mean. After assembly I slid the Mill over to the right hand side of the bench. Keeping the machine at an angle makes it easier to reach the control knobs and increases the overall bench space by using the corner
|
|
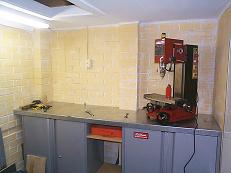
Here is a shot looking into the opening of my workshop. The length of the bench is 2.4 metres. The steel cabinets have 18mm MDF sheet on top covered by galvanised sheet metal. The front edges have been covered with 3mm x 40mm galvanised angle.
The cabinets are 1000mm high and 900mm wide. The bench is 625 mm deep.
|
September 5th, 2014
admin
I purchased this lathe on Ebay in Australia for $1650AUD delivered. I had been monitoring lathes for quite some time and finally a brand new one showed up. David runs a great business and is very efficient and has great customer skills. Most of my stuff comes from David. I highly reccomend getting this lathe as I feel it is extremely reasonably priced compared to what you may find in machinery stores.
here are the specs:
22″x10″ QUICK CHANGE GEARBOX METAL LATHE W/STAND CABINET (NEW)
*perfect for general machining in tool rooms, maintenance and production shops, cast iron quick-change gear box mkes threading easy.
*SPECIFICATION:
-SWING OVER BED:250MM (10″)
-DISTANCE BETWEEN CENTER:550MM (22″)
-SPINDLE BORE:26MM (1″)
-TAPER OF TAILSTOCK:MT2
-THREAD CUTTING: 38KINDS (METRIC & IMPERIAL)
-RANGE OF SPINDLE SPEED:6(125RPM-2000RPM)
-MOTOR:550W/240V/1PH
-GROUND AND HARDENED BED
-TOOL POST TYPE:4-WAY
-MAX TOOL SIZE:12MMX12MM
*INCLUDE:5″-3 JAW CHUCK,6″ 4-JAW CHUCK, 8″ FACE PLATE, MT2 DEAD CENTER, FIXED STEADY, TRAVEL STEADY, STAND CABINET, SPLASH GUARD, CHIP TRAY, CHANGE GEAR, TOOL ETC

The lathe has an enclosed gearbox. It has a forward and reverse switch, an emergency stop and a energise button. The energise button merely locks in the power relay that the emergency stop button releases providing the e.s button is out.
|
There is a label on the carriage. Dahhh you might say, well it’s purpose is still a mystery to me. The direction of carriage travel is subject to the direction of the motor. You can cut both ways if you like and have the carriage automatically advance.
|
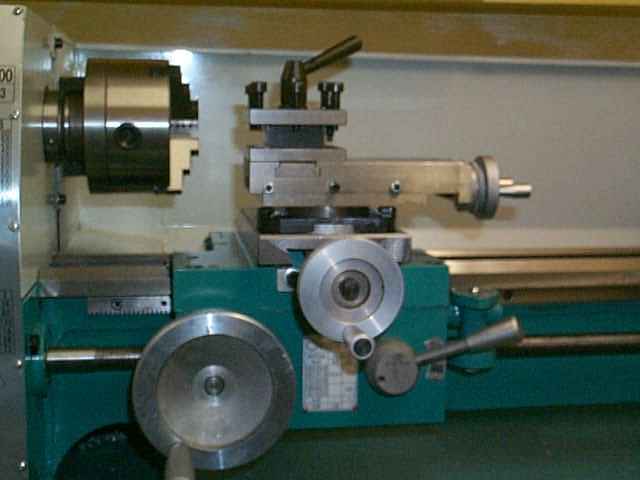
Here is a shot of the carriage near the head.
|
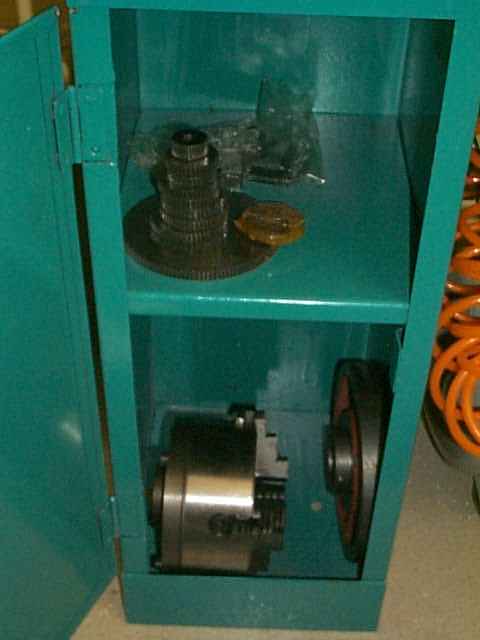
The stand was included in the price of the lathe. It came with a 6″ 4 jaw chuck, a set of reversible 3 jaw chuck jaws, a drive plate, fixed and travelling steady, dead centres, tools and change gears. I haven’t had a need to change the gears, maybe when the current ones wear out……just kidding, maybe when I need to cut some threads.
|
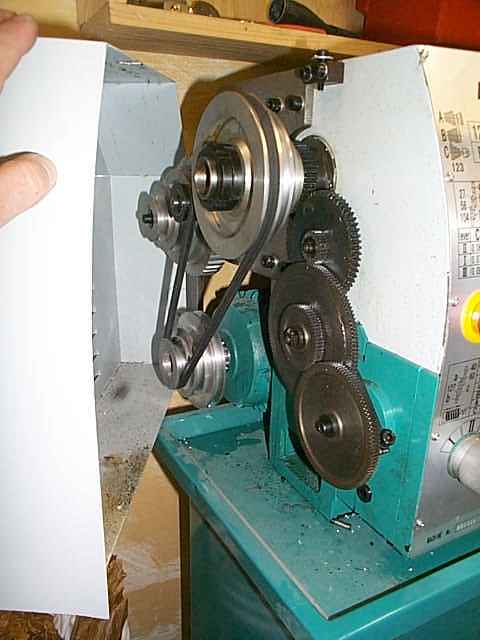
The spindle speed range goes from 150 to 2000 RPM. This is a great machine for the stuff I wish to make.
|

On my shelves I keep the toolbox along with the steadies. I also keep my shop air, don’t you just love that phrase, I should say my piss weak little compressor accessories on the shelves as the compressor is located beneath the lathe.
|
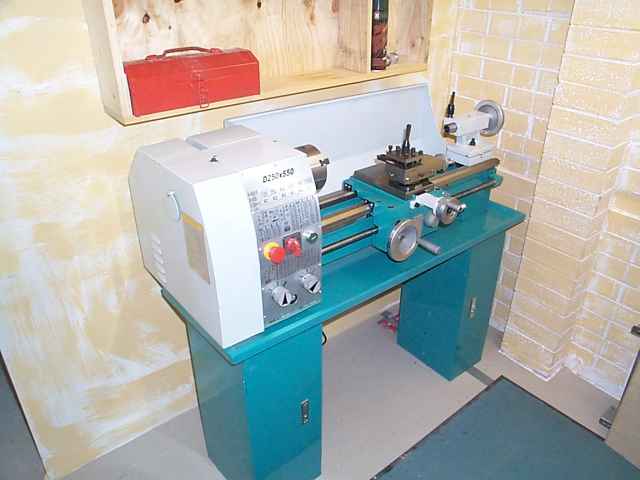
Here is an overall shot
|
Here I am trying to turn you on. Isn’t this a sexy machine?
|
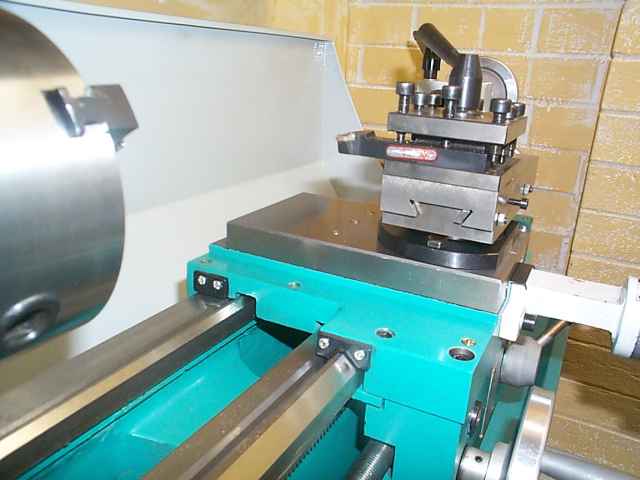
Here is a shot of the 4 way tool holder with a tool in it.
|
|